鋁型材機(jī)架加工成本控制需從原材料與工時(shí)兩大環(huán)節(jié)切入,通過精細(xì)化管理和技術(shù)創(chuàng)新實(shí)現(xiàn)降本增效。以下是關(guān)鍵策略拆解:
一、原材料損耗控制
1. 采購與庫存管理
采用ERP系統(tǒng)分析歷史用量數(shù)據(jù),結(jié)合訂單需求制定動(dòng)態(tài)采購計(jì)劃,避免過量囤積或緊急補(bǔ)貨溢價(jià)。優(yōu)先選擇標(biāo)準(zhǔn)化型材規(guī)格,減少非標(biāo)定制帶來的余料浪費(fèi)。與供應(yīng)商簽訂余料回收協(xié)議,將邊角料按比例折價(jià)返廠。
2. 智能切割優(yōu)化
引入CAD/CAM排樣軟件,根據(jù)訂單尺寸自動(dòng)生成優(yōu)切割方案,使材料利用率提升至92%以上。例如,對(duì)異形機(jī)架采用套料切割技術(shù),將不同零件嵌套排版,減少間隙損耗。建立余料數(shù)據(jù)庫,將長度≥30cm的余料分類存儲(chǔ),優(yōu)先用于小型配件加工。
3. 工藝協(xié)同設(shè)計(jì)
推行DFM(面向制造的設(shè)計(jì)),在產(chǎn)品設(shè)計(jì)階段與工程師協(xié)同優(yōu)化結(jié)構(gòu)。采用模塊化設(shè)計(jì)減少焊接節(jié)點(diǎn),通過增加通用連接件降低零件種類。實(shí)測(cè)顯示,模塊化改造可使單機(jī)架材料成本下降8%-12%。
二、工時(shí)損耗管控
1. 加工流程再造
運(yùn)用VSM(價(jià)值流圖)分析各工序耗時(shí),消除無效動(dòng)線。例如,將傳統(tǒng)"切割-沖孔-焊接-打磨"串行流程改為并行作業(yè),引入復(fù)合加工中心實(shí)現(xiàn)多工序集成,單件加工時(shí)間可縮短25%。配置快速換模系統(tǒng)(SMED),使設(shè)備換型時(shí)間控制在15分鐘內(nèi)。
2. 智能化設(shè)備升級(jí)
采用CNC加工中心替代傳統(tǒng)手動(dòng)設(shè)備,通過預(yù)設(shè)加工程序?qū)⒕日`差控制在±0.1mm內(nèi),減少返工損耗。引入視覺檢測(cè)系統(tǒng)實(shí)時(shí)監(jiān)控加工質(zhì)量,將不良品率從3%降至0.5%以下。配置自動(dòng)上下料機(jī)械臂,使有效加工時(shí)間占比提升至85%。
3. 動(dòng)態(tài)工時(shí)考核
建立標(biāo)準(zhǔn)工時(shí)數(shù)據(jù)庫,依據(jù)設(shè)備類型、加工復(fù)雜度制定差異化工時(shí)定額。例如,普通鋸切按0.2工時(shí)/米,CNC加工按0.5工時(shí)/件。通過MES系統(tǒng)實(shí)時(shí)采集設(shè)備OEE數(shù)據(jù),對(duì)偏差>10%的工序啟動(dòng)PDCA改善循環(huán)。推行技能矩陣管理,使多能工占比達(dá)到60%以上,靈活應(yīng)對(duì)產(chǎn)能波動(dòng)。
三、數(shù)據(jù)化監(jiān)控體系
搭建成本控制看板,實(shí)時(shí)顯示材料利用率、設(shè)備綜合效率、人均產(chǎn)出等18項(xiàng)關(guān)鍵指標(biāo)。每日召開10分鐘生產(chǎn)例會(huì),針對(duì)前日損耗TOP3問題制定對(duì)策。通過成本拆解模型測(cè)算顯示,實(shí)施上述措施可使綜合加工成本下降15%-22%,投資回收期控制在8個(gè)月以內(nèi)。
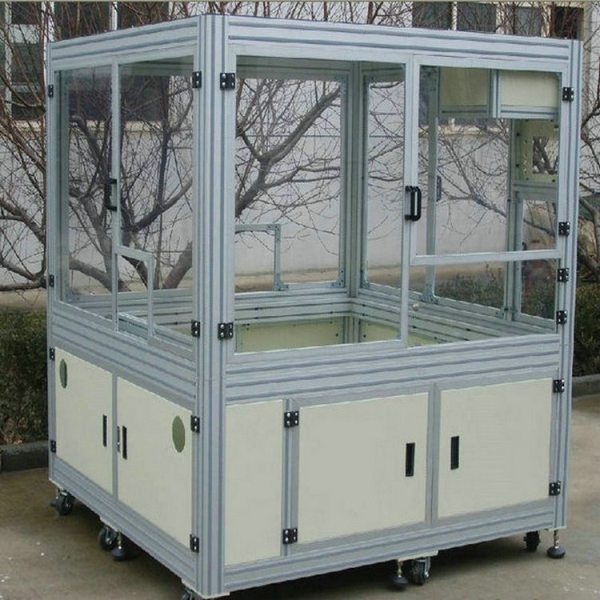